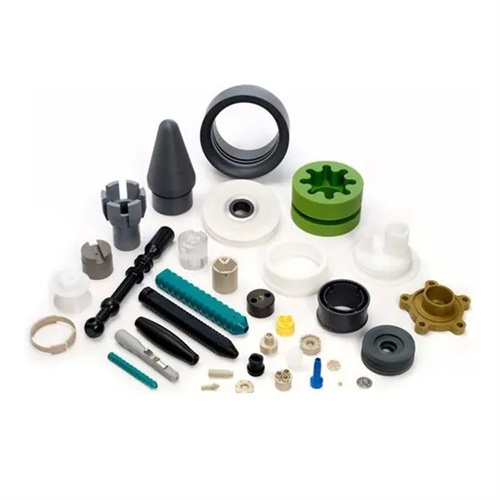
Injection Molding Parts:
As a leading manufacturer, we are deeply involved in the production of a wide range of injection molding parts, which serve as the fundamental building blocks for industries such as Hardware Tools, Electrical Appliances, Medical Devices, and Packaging. Injection molding parts play a crucial role in these sectors, enabling the creation of products with high precision, consistency, and functionality.
Injection molding parts are manufactured through a process where plastic materials, typically in pellet form, are heated until they reach a molten state. This molten plastic is then injected under high pressure into a pre-designed mold cavity. Once inside the cavity, the plastic cools and solidifies, taking on the shape of the mold. The result is a precisely formed part that can have complex geometries, depending on the design of the mold.
Types of Injection Molding Parts
Standard and Custom Parts
We produce both standard and custom injection molding parts. Standard parts are designed to meet common industry requirements and are often used in a variety of applications. For example, in the hardware tools industry, standard plastic handles for screwdrivers or pliers are produced in large quantities. These parts are made to fit comfortably in the hand and provide a good grip during use.
On the other hand, custom injection molding parts are tailored to the specific needs of our clients. In the medical devices industry, custom parts are essential. For instance, a custom-designed plastic housing for a medical diagnostic device may be required to fit specific internal components precisely and meet strict sterilization and biocompatibility standards.
Complex and Simple Parts
Our capabilities extend to producing both simple and highly complex injection molding parts. Simple parts, such as small plastic spacers or caps used in packaging, can be produced quickly and cost-effectively. These parts may have basic shapes and require minimal finishing.
In contrast, complex parts are a specialty of ours. In the electrical appliances industry, parts like the intricate control panels with integrated buttons and displays are complex injection molding parts. These parts need to be produced with high precision to ensure proper functionality. The mold design for such complex parts is intricate, often involving multiple cores and cavities to create the desired shape and features.
Manufacturing Processes for Injection Molding Parts
High-Volume Injection Molding
High-volume injection molding is a key process for us when producing injection molding parts. This process is optimized for mass production. We use high-speed injection molding machines equipped with large-capacity barrels to melt and inject the plastic. Molds with multiple cavities are designed and fabricated. For example, in the packaging industry, when producing plastic containers, a mold with 16 or more cavities can be used. This allows us to produce a large number of parts in a single cycle, significantly increasing production efficiency. The cost per part is also reduced as the initial investment in tooling and equipment is spread over a larger number of units. In the hardware tools industry, high-volume injection molding is used to produce components like the plastic housings for power tools, ensuring a consistent supply to meet market demands.
Precision Micro Injection Molding
In industries such as medical devices, where miniaturization is a trend, precision micro injection molding is of utmost importance. This process is used to produce extremely small and precise injection molding parts. Specialized equipment with high-precision injection units and molds with micro-sized cavities are employed. For example, in the production of micro-connectors for medical monitoring devices or tiny gears for surgical instruments, precision micro injection molding ensures that the parts are accurately formed with tight tolerances. The ability to work at such a small scale requires advanced manufacturing technology and highly skilled operators to control the process parameters precisely.
Liquid Silicone Rubber Injection Molding
Liquid Silicone Rubber (LSR) injection molding is another process we utilize to produce unique injection molding parts. LSR is a special type of rubber-like material that offers excellent flexibility, biocompatibility, and heat resistance. In the medical devices industry, LSR injection molding is used to create parts such as silicone catheters, which need to be flexible and safe for use in the human body. In the electrical appliances industry, LSR can be used to make gaskets and seals that provide a tight seal and are resistant to heat and moisture. The LSR injection molding process involves injecting a liquid silicone rubber compound into a mold cavity, where it cures and solidifies to form the desired part.
Two-Shot Injection Molding
Two-shot injection molding, also known as multi-shot injection molding, is a process that allows us to create injection molding parts with multiple materials or colors. In the hardware tools industry, this process can be used to create tool handles with a hard plastic core for strength and a soft-touch LSR outer layer for a comfortable grip. In the packaging industry, two-shot injection molding can be used to create containers with a clear outer layer for visibility and a colored inner layer for branding or protection. The process involves injecting the first material into the mold, allowing it to solidify partially, and then injecting the second material to bond with the first. This results in a single part with multiple properties or colors.
Applications of Injection Molding Parts in Different Industries
Hardware Tools
In the hardware tools industry, injection molding parts are used in a wide variety of products. Plastic handles for hand tools like hammers, screwdrivers, and wrenches are common injection molding parts. These handles are designed to provide a comfortable grip, reduce vibration, and enhance the user’s control. The plastic housings for power tools are also injection molded. These housings protect the internal components, provide insulation, and contribute to the overall ergonomics of the tool. Smaller parts such as gears, clips, and fasteners made from injection-molded plastics are used in the internal mechanisms of hardware tools, ensuring smooth operation.
Electrical Appliances
For electrical appliances, injection molding parts are integral to the production process. The outer shells of appliances such as refrigerators, washing machines, and microwave ovens are often injection-molded. These shells not only protect the internal components but also contribute to the aesthetic appeal of the appliance. Control panels with integrated buttons and displays are injection-molded parts that provide a user-friendly interface. In addition, internal components like brackets, spacers, and insulation parts are also injection-molded. For example, the plastic brackets that hold the circuit boards in place in a television are injection-molded for precise fit and functionality.
Medical Devices
In the medical devices industry, injection molding parts must meet strict quality and safety standards. Parts such as syringes, catheters, and medical device housings are often injection-molded. Syringes are typically made from medical-grade plastics that are sterile, biocompatible, and have good mechanical properties. Catheters made through injection molding, especially those using LSR, need to be flexible, kink-resistant, and safe for use in the human body. The plastic housings for medical diagnostic devices are designed to protect the sensitive internal components and may have features such as antimicrobial surfaces. Precision-made injection-molded parts are also used in surgical instruments, ensuring accurate and reliable performance.
Packaging
In the packaging industry, injection molding parts are used to create a wide range of products. Plastic containers, caps, and closures are common injection-molded packaging parts. Plastic containers can be designed in various shapes and sizes to hold different types of products, from food and beverages to cosmetics and pharmaceuticals. Caps and closures are injection-molded to provide a secure seal, prevent leakage, and ensure product safety. Some packaging parts may also have special features such as tamper-evident bands or easy-open mechanisms, which are achieved through injection molding techniques.
As a manufacturer, our expertise in producing injection molding parts using various processes enables us to meet the diverse needs of industries such as Hardware Tools, Electrical Appliances, Medical Devices, and Packaging. By leveraging our advanced manufacturing capabilities, we are committed to delivering high-quality injection molding parts that contribute to the functionality, safety, and aesthetics of products in these industries.