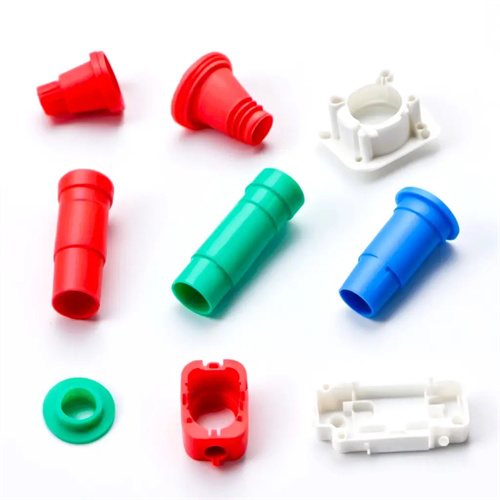
High-Volume Injection Molding
In today’s competitive marketplace, the ability to produce large quantities of high-quality parts is crucial for businesses. High-volume injection molding offers several key advantages. Firstly, it provides significant cost savings. The initial investment in tooling and equipment is spread over a large number of parts, reducing the per-unit cost. This makes it an ideal choice for industries with high-demand products, such as toys, where millions of units of a popular item may need to be produced. Secondly, high-volume injection molding ensures consistent quality. Once the process is optimized, each part produced is virtually identical in terms of dimensions, material properties, and surface finish. This consistency is essential for industries like hardware tools and electrical appliances, where precision and reliability are non-negotiable.
As a leading manufacturer, high-volume injection molding is one of our core competencies, enabling us to meet the demands of industries such as Toy, LED Lighting, Hardware Tools, and Electrical Appliances. This advanced manufacturing process has revolutionized the production of injection molding parts, allowing for efficient and cost-effective mass production.
The Manufacturing Process of High-Volume Injection Molding
Design and Tooling
The journey of high-volume injection molding begins with meticulous design. Our team of experienced engineers uses state-of-the-art computer-aided design (CAD) software to create detailed 3D models of the injection molding parts. When designing for the toy industry, for example, we consider factors like playability, safety, and aesthetic appeal. In the case of LED lighting, we focus on optical properties, heat dissipation, and form factor.
Once the design is finalized, the tooling phase commences. High-volume production requires molds that are robust and durable. We use high-quality steel or aluminum to fabricate molds, often with multiple cavities. Multi-cavity molds are a game-changer in high-volume injection molding. For instance, in the production of small plastic components for hardware tools, a mold with 32 or even 64 cavities can be designed. This allows us to produce dozens of parts in a single injection cycle, significantly increasing production efficiency. The molds are engineered with precision to ensure that each cavity produces a part that meets the exact specifications.
Material Selection
Choosing the right plastic material is a critical step in high-volume injection molding. In the toy industry, materials like acrylonitrile butadiene styrene (ABS), polypropylene (PP), and polyethylene (PE) are commonly used. ABS offers good impact resistance and a high-quality surface finish, making it suitable for toys that may be subjected to rough play. PP is lightweight, cost-effective, and has excellent chemical resistance, which is ideal for toys that come into contact with various substances.
For LED lighting, materials with high light transmittance, such as polycarbonate (PC), are preferred. PC allows for efficient light diffusion, enhancing the performance of the lighting product. In the hardware tools and electrical appliances industries, materials like nylon are used for their high strength, wear resistance, and heat resistance. Nylon is often used for gears, fasteners, and other components that need to withstand mechanical stress.
Injection Molding Process of High-Volume Injection Molding
Our state-of-the-art injection molding machines are the workhorses of high-volume production. These machines are equipped with large-capacity barrels to melt and inject the plastic. The plastic pellets are fed into the machine’s hopper and heated to a molten state. The molten plastic is then injected into the mold cavity under high pressure. The pressure ensures that the plastic fills every intricate detail of the mold, accurately replicating the design.
For high-volume production, we often use high-speed injection molding machines. These machines can cycle quickly, reducing the time between each injection. The cooling time is carefully controlled to ensure proper dimensional stability of the part. Different plastics have different cooling requirements, and our expertise allows us to optimize this process for each material. For example, some plastics may require rapid cooling to prevent warping, while others need a more gradual cooling process to achieve the desired material properties.
Quality Control of High-Volume Injection Molding
Quality control is an integral part of high-volume injection molding. We have implemented a rigorous quality management system to ensure that each part meets the highest standards. Every part undergoes inspection for dimensional accuracy, surface finish, and structural integrity. In the electrical appliances industry, where product safety is crucial, we perform additional tests to ensure that the parts are electrically insulated and can withstand the intended operating conditions.
We use automated inspection systems for high-volume production. These systems can quickly detect any defects, such as cracks, warping, or incorrect dimensions. Defective parts are immediately removed from the production line, preventing them from reaching the end-customer. This not only ensures the quality of our products but also helps us maintain high production rates without sacrificing quality.
Applications of High-Volume Injection Molding
Toy
In the toy industry, high-volume injection molding is used to produce a wide variety of toys. Action figures, building blocks, toy vehicles, and dolls are all commonly made through high-volume injection molding. The ability to produce large quantities of toys allows toy manufacturers to meet the high demand during peak seasons, such as Christmas. For example, a popular action figure may require the production of millions of units. High-volume injection molding enables us to produce these figures with consistent quality, ensuring that each toy looks and feels the same.
The process also allows for the creation of complex designs. Toys can be molded with intricate details, such as facial expressions on dolls or detailed body armor on action figures. In addition, high-volume injection molding can be used to produce toys with multiple parts that fit together perfectly, like building blocks or modular toys.
LED Lighting
In the LED lighting industry, high-volume injection molding is used to produce components such as light diffusers, lamp housings, and heat sinks. Light diffusers are crucial for evenly distributing light from the LEDs. High-volume injection molding allows us to produce light diffusers with precise optical properties, ensuring optimal light output. Lamp housings are also injection-molded in large quantities. These housings protect the LED components and contribute to the overall aesthetic of the lighting product.
Heat sinks are another important component in LED lighting. High-volume injection molding can be used to produce heat sinks with complex geometries that are designed to dissipate heat efficiently. By producing these components in high volumes, we can help LED lighting manufacturers reduce costs and bring more affordable, high-quality lighting products to the market.
Hardware Tools
Hardware tools rely heavily on high-volume injection molding for the production of various components. The handles of screwdrivers, pliers, and hammers are often injection-molded from materials like rubber-coated plastics or soft-touch polymers to provide a comfortable grip. Tool housings, such as those for power drills and circular saws, are also made through high-volume injection molding. These housings protect the internal components and provide a durable and ergonomic exterior.
Smaller internal components, like gears, clips, and fasteners, are produced in high volumes to meet the demands of the hardware tool market. For example, the plastic gears used in the internal mechanisms of a power drill are produced in large quantities to ensure a consistent supply. High-volume injection molding allows for the production of these components with high precision, ensuring smooth operation of the tools.
Electrical Appliances
In the electrical appliances industry, high-volume injection molding is used to produce a wide range of parts. The outer shells of appliances such as refrigerators, washing machines, and microwave ovens are often injection-molded. These shells not only protect the internal components but also contribute to the aesthetic appeal of the appliance. Control panels with integrated buttons and displays are injection-molded parts that provide a user-friendly interface.
Internal components like brackets, spacers, and insulation parts are also produced through high-volume injection molding. For example, the plastic brackets that hold the circuit boards in place in a television are injection-molded for precise fit and functionality. High-volume injection molding enables electrical appliance manufacturers to produce large quantities of these parts at a lower cost, making their products more competitive in the market.
As a manufacturer, our expertise in high-volume injection molding allows us to provide high-quality injection molding parts to industries such as Toy, LED Lighting, Hardware Tools, and Electrical Appliances. By leveraging advanced design, tooling, material selection, and quality control processes, we are able to meet the high-volume production needs of our clients, contributing to the growth and success of these industries.